CMP Drill Rifle Initiative Receivers
Laboratory Testing, Inspection Controls, and Integration into Regular Rifle Production
Civilian Marksmanship Program • Anniston, Alabama • 24 April 2025

Program Overview
The Civilian Marksmanship Program (CMP), in cooperation with Heritage Arms USA (Oxford, Alabama) and Prospector Training LLC (Crawfordville, Florida) has completed a comprehensive engineering program to determine whether weld-repaired drill-rifle receivers for the M1 Garand and Model 1903-A3 can return to live-fire use while meeting the same safety and durability standards as original receivers. Heritage Arms performed the weld removal, machining, and assembly of the test rifles while Prospector Training executed the proof-firing and destructive metallography and supplied quality-engineering support.
The investigation quantified pressure strength after reclamation, monitored dimensional stability under proof-level loads, evaluated micro-crack behavior at weld sites, and established a production scale inspection method capable of screening every receiver for subsurface indications. A permanent archive of dimensional data, firing logs, metallography data, and inspection results is maintained for every unit to protect product-stream integrity.

Test Material and Procedure
Eighteen receivers representing all weld configurations in CMP storage were refurbished to U.S. Ordnance drawings and divided into two metallurgical groups:
- Case-hardened – preserved in original factory heat-treat
- Fully annealed – intentionally softened to create a worst-case baseline
Baseline thread-ring length, minor diameter, and head-space were logged to ±0.0001 in.; surface magnetic-particle inspection confirmed no open cracks before assembly. The receivers were barreled and chambered to SAAMI-minimum .30-06 specifications (with comparable chambers for 1903-A3 units).
Each rifle was fired from a rigid fixture in three stages:
Stage | Rounds | Approx. Peak Pressure | Purpose |
Break-in | 7 Ball | ~50 000 psi | Seat components and establish thermal equilibrium |
Proof | 3 Over-pressure | ≈ 82 000 psi | Evaluate strength 64 |
Post-proof | 7 Ball | ~50 000 psi | Verify function after proof shock |
Post-fire dimensional audits repeated baseline measurements to determine the presence of any growth or deformation driven by the extreme pressures of proof firing. Both metallurgical categories were evaluated comparatively to determine the degree of effect that any compromise to the heat treat might have on the receiver’s ability to withstand pressure.

Mechanical Findings
- Head-space change: maximum permanent growth 0.003 in.
- Head-Space Delta by Average of Metallurgical Category: .00025
- Structural integrity: no lug setback, rail deformation, or receiver-ring expansion
- Failures: zero catastrophic or partial failures after proof-level rounds
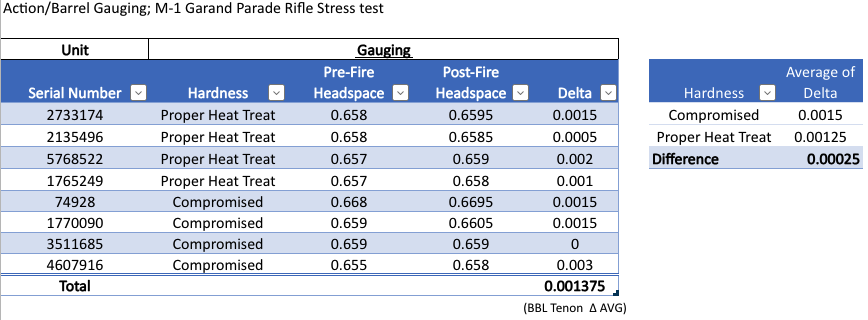
Pressure testing under proof loads far exceeding standard limits reveals that the welding present on the reclaimed receiver has not reduced their capacity to contain pressure. The results are further supported by comparable dimensional observance between properly heat-treated receivers and those that were completely and intentionally compromised. The difference in average delta in deformation between the sample categories proved to be less than .001” and still within serviceable limits, despite being subjected to pressures 60% above what will be generated under normal conditions.

Microscopic Findings
Sectioned receivers displayed heat-affected zones 0.040 – 0.060 in. wide and a single occurrence of hairline cracking of ~0.004” magnitude at a weld perimeter. The occurrence suggests the likely presence of subsurface cracking in no more than seven percent of the total inventory. While no crack propagation or branching was detected after the 82 kpsi proof series, the mere presence of these latent flaws drove CMP’s decision to implement a production-scale, non-destructive solution capable of interrogating every finished receiver for similar indications. This requirement became the basis for adopting dual-field wet magnetic-particle inspection across the entire line.

Production-Line Inspection Controls
CMP applies dual-field wet magnetic-particle inspection (MPI) to every drill-rifle receiver, detecting surface and subsurface discontinuities ≥ 0.002 in.:
- A positive indication triggers immediate segregation.
- Engineering review may authorize weld repair followed by re-inspection.
- Receivers that cannot be cleared are permanently removed from production.
All inspection data and pass/fail outcomes are logged to each serial number, ensuring lifetime traceability.

Integration with Existing Rifle Grades
Receivers that pass wet MPI and final gauging feed directly into CMP’s standard Service, Field, and Expert grade rifle production. They are not labeled, priced, or warrantied differently from current offerings as assembly procedures, quality assurance, and safety inspections remain unchanged. CMP maintains that each of these products is of equal quality and safety, regardless of receiver provenance, and will extend no offer to further identify units associated with the project.

Evidence of Repair and Finish
CMP acknowledges that the drill welds and reclamation process may cause slight color variation in the manganese-phosphate finish.

Summary for Customers
Proof firing at ≈ 82 000 psi produced negligible dimensional shift and no structural failures, while microscopic evaluation confirmed that weld-zone cracks remained static. Acknowledging and addressing the likelihood of subsurface fracture, comprehensive wet MPI has been employed to remove any receiver with a subsurface indication. All tested and defect-free units will integrate into CMP rifle grades while meeting the functional and safety benchmarks established for original actions.

Conclusion
The Drill Rifle Initiative demonstrates CMP’s commitment to preserving historic firearms while upholding modern safety standards. Rigorous proof testing, microscopic analysis, and 100 % wet-MPI screening confirm that weld-repaired receivers retain pressure integrity comparable to untouched originals. By archiving every measurement and inspection result, CMP maintains transparent quality oversight from refurbishment to sale.
For collectors, these efforts keep authentic U.S. receivers in circulation rather than consigning them to scrap. For competitors and recreational shooters, they sustain rifle availability without altering grades, prices, or warranty terms. Most importantly, the initiative advances CMP’s Congressionally mandated mission: expanding marksmanship opportunities, promoting firearms training and safety—especially among youth—and preserving America’s military heritage. Through technical rigor and historical stewardship, the Drill Rifle Initiative exemplifies how that mission is executed for shooters across the nation.